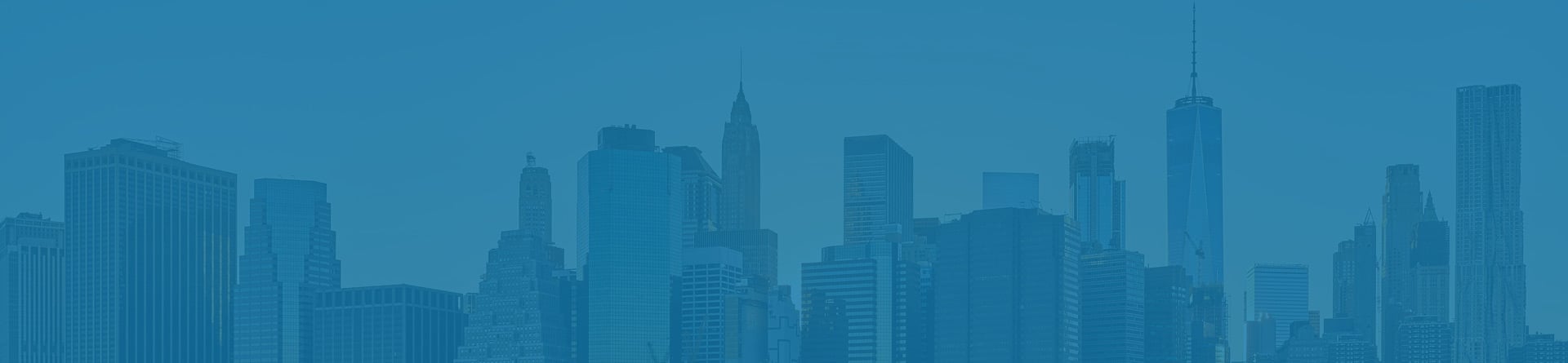
Backflush Costing
It is a delayed product cost accounting process
Backflush Costing, also called Backflush Accounting, is a delayed product cost accounting process. This means the accounts are made once the products are finally sold, and services are completed.
The costs associated with raw materials used in the process are not accounted for separately but are counted together, thus merging all costs after the production process is finished.
Towards the end of the process, it eliminates the need for full-scale tracking of all the expenditures incurred, hence making the task of recording the accounts less comprehensive.
This method eschews the usage of work-in-progress accounts and the effort of looking into each material account at different stages of production to assess the costs, thus making the job easy.
It requires a lot of time and cost for a company to record entries owing to which some choose to save all the entries throughout the process of manufacturing a product or rendering a service and "flush" them into a single entry when it is done.
Since this entry was not recorded at the time the inventory was being used, accountants are required to use standardized or normal costing methods to record the entries thereby.
This process helps the costs work their way backward to the raw materials.
In this way, the costs are "flushed back" to the account of the raw materials used to produce that finished product.
This method is suitable for products with complex production processes requiring different manufacturing stages in their production span.
This can mean that the single entry accounts for more than fifty or even one hundred entries! In such cases, it becomes practically impossible to record each entry with the incoming of each raw material.
Let us look into the different aspects of Backflush Costing in the next sections.
JIT and backflush costing
Now you may wonder why we don't just increase the entries by a few numbers and use the conventional method of accounting instead of the Backflush method.
Well, there is one reason; all organizations have limited resources. They strive to achieve maximum effectiveness using these limited resources to save themselves from future unexpected losses.
Backflush Costing comes into the picture because it eases the process of maintaining the cost records. Backflush Costing is prevalent among those organizations that follow Just-in-Time Inventory Management System.
A Just-In-Time style of inventory, also known as the Toyota Production System (TPS), is an inventory management system that aims to keep and store as many goods as the actual demand requires.
This allows the company to avoid maintaining regular accounts for tracking stock movement in and out of their storage facilities.
The JIT helps companies in the efficiency of operations and minimizing wastage costs. This way, the raw materials that would have been used to cover up for unexpected orders are not being used, which helps the company cut unnecessary costs.
Recording entries right from the arrival of the raw materials until the product is manufactured is a tedious task.
We create raw materials account to obtain the raw materials, which are then transferred to the work-in-progress account. Once the production cycle is complete, it is finally transferred to the finished goods account.
Under the Backflush Model, raw materials are ordered only when needed, making it comparatively less of a task to account for all the orders at the end of a specific period altogether.
Whereas, under the conventional method, many heads are created for the same stock of materials like labor costs, overhead costs, transportation expenses, lodging costs, etc.
Next, they are moved to the WIP, from where they are moved to the processing stage, and other costs required are added. Then finally, they are moved to the Finished Goods and later on to the Cost of Goods Sold (COGS).
Backflush costing process
Now, we will look into the step-by-step process that this method follows. It is no different than a simple accounting process generally followed by companies.
First, the company receives an order from the customer and records only the information (quantity, delivery date, raw materials, item code, etc.) that is necessary at the time.
This information is fed to the system, and the cost manager is set to tick off all the items on the list so that the order is ready by the desired date.
The company orders the exact quantity of raw materials required, neither more nor less than what is needed.
The software keeps tracking the raw materials, and the cost managers monitor the process, directing whether to place orders for more raw materials.
Orders are placed for the components needed to keep the production process going. After the production is done, all the details are accounted for in the software, and a production report is prepared.
According to the report formed, the material costs are assigned to each component used during the making of the lot, and a single entry is entered, accounting for the whole operation.
This process shows how a business can save a lot of resources in the form of time and funds using this method.
Journal entry
The journal entry for Backflush Accounting is very simple to account for, as it is a single entry reckoned at the end of the production process.
It is based on the standard cost allotted to the raw materials over time and the quantity of the units produced.
Let's take a basic example to get the primary understanding of how a backflush account is created.
Suppose a manufacturer of a company that sells personalized and custom products wants to record a single entry for all the components they ordered until the product is finished.
The order needs to be shipped to the customer by January 31st. Let's assume he paid through the check.
The journal entry would look like the following:
Date | Particulars | Debit (in $) | Credit (in $) |
---|---|---|---|
January 31st | Components A/c | 1500 |
|
| To Bank A/c |
| 1500 |
This entry will be recorded on the 31st of January, as the backflush accounts are closed only when the product is finished and sold.
Now think if there would have been too many different types of components used in the production of this product, recording these entries would have been a time-wasting task for the owner if it weren't for backflush accounting.
Let's assume there were five major components used to make this product. The accounting would look like this:
Date | Particulars | Debit (in $ | Credit (in $) |
---|---|---|---|
December 15th | Component 1 A/C | 150 | |
To Bank A/c/C | 150 | ||
December 27th | Component 2 A/C | 29 | |
To Bank A/c | 29 | ||
January 7th | Component 3 A/C | 165 | |
To Bank A/c | 165 | ||
January 19th | Component 4 A/C | 1150 | |
To Bank A/c | |||
January 25th | Component 5 A/C | 6 | |
To Bank A/c | 6 |
As it can be seen, recording multiple entries is a tedious task as well as time-consuming for the manufacturer.
Moreover, each of these entries would be recorded at the respective dates when the components were bought, which is not required, considering the company follows a Just-in-Time inventory management system.
Why is it used?
Backflush costing is used by businesses that have a very high turnover rate in their inventory.
Inventory turnover is the frequency with which the inventory is sold or used in a time period. This shows that the company has a strong customer base with frequent orders with almost no time gaps.
This means that the company has a good financial standing with respect to receiving orders from its considerably strong customer base.
In other words, the company sells goods quickly, and there is a constant demand for its products. This is another explanation for Just-in-Time inventory management.
It is a convenient method for businesses with many distinct costs that follow the production process. The accounting department, thus, saves a lot of sweat by recognizing standardized costs for the materials used.
For example, a manufacturer estimates the standardized cost to be $45 for each material. The total number of products produced is 500 units. Now, when the production is done, and goods are sold, a journal entry of $22,500 will be made.
One may think that since this method is so automated, it must be arduous to track the costs in a backward fashion.
But to our surprise, a very simple formula aids us with the cost assignment process. It is expressed as the relationship between the total production and the total units of components.
R = T*C
Here, 'R' implies the units of raw materials issued from the warehouse for use in the production, 'T' refers to the Total Production, and 'C' is the count of the listed components in the materials bills used.
Not only this, but this method of accounting makes the issuance of the materials much easier. Issuing materials means acquiring raw materials from the warehouse using a proper authorization process, including documentation.
Owing to these reasons, this method is very popular among companies with complex manufacturing processes.
Limitations and advantages
As much as the method of Backflush Accounting is attractive in theoretical terms, it may not be easy to implement it in real life.
1. Since companies with fast production pace and high turnover of inventory level employ this method, they need to make sure that all the costs incurred throughout the production process are maintained on a standardized basis.
2. By keeping the costs standardized, we can avoid obtaining the discrepant bill of materials (which consists of two segments, the production count and the raw materials and components, and their standardized costs).
This prevents the business from running short on resources such as time and costs of recording.
3. The Backflush Costing method allows companies to compute the true and complete costs of the products after they are finished as they record all the costs associated with that product all at once, at the end.
Besides all the disadvantages, this method saves a lot of costs that may be an attractive opportunity for any company, thus overlooking all the other cons.
This method is the most helpful when it comes to efficiency, but every great thing comes with a cost.
This method of accounting usually does not conform to the General Accepted Accounting Principles (GAAP). Thus, this can make the auditing process for the companies a difficult task to achieve.
This happens because it makes it difficult to trace the costs of each component used in manufacturing that particular product as all the accounts now has been merged within one.
However, this does not rule out the convenience of this method. Many companies follow this method without any hurdles.
The companies employing this method need to compute a "standardized cost" for the units produced. This method through which the costs are traced back is called "sequential tracking."
In the real world, the companies using Backflush Costing need to recognize the variations in standardized and actual costs.
For example, we are comparing the total raw materials being ordered by the factory and the raw materials ordered for the production run of that good.
Key Takeaways
Backflush Costing, also known as Backflush Accounting, is a method that allows us to allot an accumulated cost to a finished product's account.
This means that all the costs associated with that one product are recorded once when the manufacturing process of the product ends.
Businesses that have a plethora of costs associated with a product or good, which takes comparatively less time to assemble, seek to follow the rules of Backflush Accounting.
However, it is not necessary that this method works out for companies selling personalized and customized products.
Adding on to the previous point, this method is most suitable for organizations that follow the Just-in-Time inventory management system.
This method has some significant pros and cons. This method comes under Lean Management.
At the same time, it makes the task of auditing cumbersome as tracking costs might appear to be difficult.
Backflush Costing uses the standard cost per unit of the product produced and this cost obtained is then multiplied by the total number of products manufactured to get to the total expenses incurred.
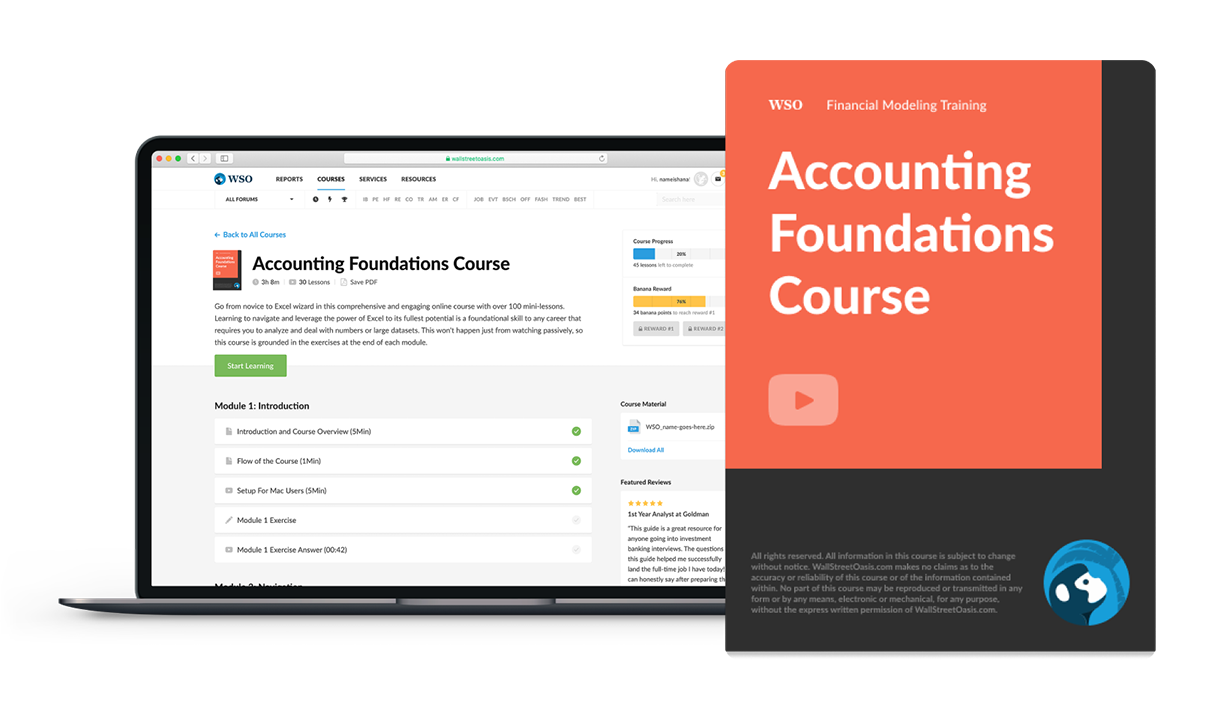
Everything You Need To Build Your Accounting Skills
To Help You Thrive in the Most Flexible Job in the World.
Researched and authored by Anushka Raj Sonkar | Linkedin
Free Resources
To continue learning and advancing your career, check out these additional helpful WSO resources:
or Want to Sign up with your social account?